A Rapid Response Science Support Team
Mobilizing Capabilities to Resolve Big IssuesCase Study
A key raw materials supplier discovered a high-risk quality compliance gap that could affect several high-profile brands for a Fortune 50 consumer goods giant. The supplier was directed to shut down their newly-opened production line until the risk could be resolved, costing the consumer goods company $1 million per day. ATL’s Rapid Response Support Team was called to develop a resolution strategy, fix the problem, and help the supplier resume production within compliance standards.
Action
ATL received the call late Friday evening—we had three days to have resources in place to avoid production and release delays. The next day, we were on a plane to the client site. We partnered with the client to find and assess the quality gaps and create an operational strategy. Our role was to resolve any method-related issues impacting quality or release timing and implement processes and procedures to bring the entire production line into compliance.
Results
- Improved all quality systems to cGMP level compliance.
- Optimized methods by eliminating results variability and increasing productivity.
- Saved $1 million per day in production down time and waste.
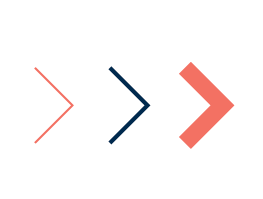